Hydraulic Style Linkage
Hydraulic clutch linkage systems have moved into dominance in the past two decades, and generally with good reason.
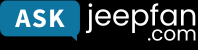
Get personalized content recommendations and answers drawn from our website. Simply type your question or topic of interest, and our AI assistant will help you find relevant articles, tips, and insights. You can also have a natural conversation to explore topics in more depth.
The most common rendition of this linkage consists of the pedal pushrod against a master piston / cylinder, a high-pressure tube or line and a slave piston / cylinder whose pushrod pushes the clutch release arm.
A less common style of hydraulic release is the internal hydraulic release bearing. This design combines the piston and bearing into one unit, eliminating the pivot, fork (or release arm) and separate throwout bearing.
Jeep Internal Hydraulic Throwout Bearing (left) A Jeep internal hydraulic throwout bearing, common in YJ Wranglers and XJ Cherokees between 1987-1994.
They are innovative in design but have gained notoriety for leak failures. Hardened o-rings are usually the culprit, and this occurs as much from non-use (drying out) as overuse (abrasion wear).
To add serious insult to significant injury is to have the failure prone Peugeot transmission (1987-1988) with a bad internal release bearing.
A word is in order at this point about hydraulic clutches and the misconceptions that surround them. Many individuals believe that it is the interaction of the hydraulic master and slave cylinders through which the force against the clutch pressure plate is multiplied. In fact, the actual multiplication of force occurs in two different areas of the clutch system. First it is in the leverage of the clutch pedal assembly. The master cylinder actuator being closer to the fulcrum of the pedal arm, distance is reduced and force is increased, through that great principle of physics with which all mechanically minded individuals are aware. Secondly, additional force is created through the leverage of the clutch release arm. In basic principle, this is the way clutches have been virtually since the inception of the automobile.
![]() This is an aftermarket internal hydraulic throwout bearing. The drawback is the expense, at over $300 |
The hydraulic system, therefore, is simply a method of transferring that leverage – or better said, of transmitting force through the incompressable hydraulic fluid. This is very similar in principle as a good old mechanical linkage via pushrods, bellcranks or cables. Essentially no multiplication of force occurs within the hydraulic circuit itself as is common with other hydraulic systems like jacks, rams and presses.
This leads to the next useful principle: Nearly every clutch master cylinder is matched for size to its connected slave cylinder for a largely 1-to-1 relationship. So, a 3/4″ bore master cylinder should connect to a 3/4″ slave cylinder. A 1″ master should have a 1″ slave cylinder. A master cylinder that is larger will yield a rather spectacularly blown out slave cylinder and a master cylinder that is smaller will yield a rather disappointing lack of travel for your left foot’s efforts. There are occasions where this ratio can vary slightly from this, but rarely more than 15%.
Once the installer understands this, the rest will come together more easily and in accordance with the principles outlined for conventional mechanical clutch systems.
Hydraulic systems can be simple, but mostly when there are existing provisions for mounting the master and/or slave cylinders. Thin firewalls and bellhousings without proper structural provisions for slave cylinders are the chief entanglements that hamper retrofit.
Sequence of Linkage Setup
Let’s assume we are using a Chevrolet engine, Rockford clutch (diaphragm type), and the back of the block is “bare” but the crankshaft is in the block.
Install the pilot bushing to be used for the particular engine-transmission combination in the crankshaft. Then, with a suitable dial indicator, check the bore of the pilot bushing. Runout should not exceed .002 (two thousandths) of an inch.
Temporarily install the bellhousing to be used on the block it will be used with. (This is important as the results of this test can vary with a different block or bellhousing.) Test the bellhousing for “runout” on both its bore and face as described in the trouble-shooting section. Bore runout must be within .007″ and face runout to within .004″. If you don’t, can’t, or won’t check bellhousing alignment, do not be surprised if you have problems. These will not show up right away. It may be several thousand miles before a clutch hub, pilot bushing, or transmission fails.
Temporarily bolt the transmission to the bellhousing. Look through the release fork opening to determine that the pilot area is at least 3/8″ engaged into the pilot bushing bore. If it is not, the pilot bushing is incorrect and a longer bushing must be installed, or in some cases, the bushing can be installed at less than full depth.
Remove the transmission and bellhousing. Install the flywheel on the engine. Most engines use grade 8 (high-strength) bolts with a special low profile head to clear the disc hub. Do not substitute regular bolts for these special bolts.
Check the face of the flywheel for runout with a dial indicator. Runout should not exceed .005″. If it does, the flywheel should be resurfaced. If runout exists after resurfacing, the fault is either in the resurfacing job or there are burrs, dirt, or dings on the crankshaft or flywheel hub. Remember there is end play in the crankshaft bearings and this must be held in one direction when checking flywheel runout (or bellhousing face runout).
Install the clutch disc and pressure plate on the flywheel. Use a clutch aligning tool or the transmission itself. This is important as it will simplify transmission installation and prevent assembly damage. Tighten the mounting bolts 1/4 turn at a time so as not to distort the clutch cover.
Choosing a Release Arm
Stay alert on this step. Things get kind of involved but it is very important. The release arm must be the same ratio as the arm that was originally in the Jeep for the linkage to work. Notice we said ratio, not length. Assume the release arm is the typical rocker type with its pivot between the release bearing and the linkage attach point and figure the ratio as follows.
Measure the Jeep arm from the pivot point to the center of the clutch release bearing. Also, measure the distance from the pivot point to where the linkage attaches. Divide the inner length into the outer length to obtain the ratio of the arm. (Example: A stock Jeep arm from a 1976 CJ5 measures 3.1″ from the pivot in and 6.2″ from the pivot out to where the linkage pushes. Divide the 3.1″ into 6.2″ and you find this arm has a 2-to-1 ratio. This means if you move the end of the arm 1″, the release bearing would have to move 1/2″ in the opposite direction.)
Now assume we need a Chevy arm to work with this same linkage. Chevy arms all measure 3″ from the pivot in. We need a 2-to-1 ratio (as this is what the Jeep linkage and many GM pressure plates are designed for) on the Chevy arm so we require a Chevy arm 6″ long from the pivot out. Unfortunately no such Chevy arm exists. The shortest non-hydraulic arm is 6.5″ from the pivot out. Some are as much as 9″ pivot out. The short arm is 2.17 to 1 and the long arm is 3 to 1. The long arm must be shortened 3″ to be compatible with the linkage. What about the short arm? You could make it work on this particular vehicle by sacrificing some free play (at the release bearing) as well as air gap at the disc (full release condition). This particular short Chevy arm also has an end shape that is correct for the Jeep linkage we used as an example. This 6½” long Chevy arm is available from Novak as our #RAGM.
All of this changes when a vehicle with different style original linkage is being worked on.
The early style CJ’s (pre-1971 with 4 cylinder) for example, had a very short release arm; the remaining leverage occurs additionally in the linkage system. However, if this arm is measured from the pivot in and divided into the pivot out length it will be found to have a ratio of 2.4″ to 1. As previously stated, there is no factory GM release arm with the required outer length that has the proper type end. A longer arm can be shortened and the end modified to accept the Jeep linkage. However, Novak has these arms available as our #RAV6.
From all this, it should be observed that the release arm to be used with a conversion will sometimes have to be modified to get the proper ratio and this must be done at the start of the installation. Trying to use an arm that is too long will result in problems that cannot be corrected with changes in linkage.
GM Clutch Release Bearings
The following procedure should help you to determine which of the six different length clutch release bearings you will need to properly operate the clutch.
Let’s assume we are still working with a 10½” or 11″ Rockford (diaphragm type) clutch on a GM engine. Other makes of engine, Ford or Jeep for example, or a Borg and Beck (3 finger type clutch) procedure would be same with exceptions that we will mention later.
Install the flywheel (always have it resurfaced before this procedure), clutch disc, pressure plate and clutch housing on the engine. Be advised that there can be NO oil or grease on your hands, the flywheel or pressure plate friction surfaces, or on the clutch disc. If there is, the clutch will grab (chatter) when being engaged.
Install the correct length clutch fork on a 1½” long pivot that has the correct head type for the retainer on the fork (refer to fork and pivot information previously discussed). Position the fork so it sticks out of the clutch housing at about 4 or 5 degrees less than a right angle with the engine centerline (this would be when looking down on the engine from above—the fork should be ahead of, or less than a 90 degree angle by 4 or 5 degrees). Hold the fork at this angle and measure from the inner front thrust surfaces of the fork to the diaphragm spring (or fingers) of the clutch. Choose a release bearing length from the “A” dimension in the chart below that is closest to the measured length.
-A- Length | -B- Overall Length | Part Number |
3/4″ | 1-17/64″ | N 4068 |
15/16″ | 1-5/8″ | N 1741 |
1″ | 1-41/64″ | N 2001 |
1-1/16″ | 1-11/16″ | N 1466 |
1-1/4″ | 1-7/8″ | N 1086 |
When measuring, try to keep the inner ends of the fork parallel with the clutch—it is possible to be off as much as 3/16″ if not parallel.
Question about the internal hydraulic throwout bearing, can that be retained when swapping in a 350? Or are shims needed?