Clutch Release Bearing
As its name implies, this is the bearing that releases the clutch. It is often referred to as a “throw-out” bearing. They come on a number of different style carriers. The carriers, in some cases, vary considerably with the particular engine. In the GM line, for example, the bearings are all the same but there are several different carriers that vary about 1/2″ between the shortest and longest. Which to use usually depends on the style of pressure plate being used, but substituting one length for another can often be used to the installer’s great advantage. AMC, Ford & Mopar and others are far less generous with the variety of lengths available. This will be covered in more detail later in this article.
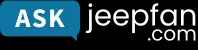
Get personalized content recommendations and answers drawn from our website. Simply type your question or topic of interest, and our AI assistant will help you find relevant articles, tips, and insights. You can also have a natural conversation to explore topics in more depth.
Because the release bearing only works when the clutch is being released it usually lasts quite a long time. However, improper linkage adjustment or riding the clutch with your foot when driving can wear the bearing prematurely. Normally there should be a minimum of 1/16″ clearance between the face of the bearing and the three release fingers or diaphragm spring of the pressure plate when the clutch is engaged.
This fact is important and will be discussed further when we get to the part about setting up the clutch linkage.
Clutch Release Fork
This is the arm or lever that the linkage operates that moves the release bearing. There are several different styles of release arm. The most common in automotive use is the fork type that pivots on a rocker. This type requires a rearward force to move the release bearing forward. Note now that the following is key to your understanding of the clutch system: The ratio of the arm is the difference in length between the pivot point and the release bearing centerline divided by the length from the pivot point to where the linkage attaches. The ratio of the fork is important and will be used in the linkage setup section later in this article.
GM, Ford, and AMC all use a pivot type release arm as their most common type. Some late GM, Pinto, Jeep and a few others use a non-rocker arm. This style pivots on the passenger side of center and is direct acting. That is, it takes a forward movement of the linkage to move the release bearing forward. This is not as suitable as the rocker system as it usually complicates the linkage requirements.
Regarding GM clutch forks, there are two basic types of manufacture used for the pivot type forks. These are stamped steel and forged steel. The stamped steel type uses a flat steel retainer spring that is riveted to the fork. These forks must be used with mushroom-head type pivots. The forged steel forks must use the ball-head type pivot. (This is different than the ball-on-pedestal AMC type.) These forged forks are retained on the pivot by a spring-wire retainer that fits in a groove machined in the ball pocket in the fork.
Release Arm Pivot
As its name implies, this is the support that the release arm pivots on. There are basically two types. One pivots on a ball-ended stud that screws into the bellhousing. The other type is an actual bearing ball that sits in a pedestal type socket that is part of the bellhousing. GM, Ford, and early AMC use the screw-in type. Late AMC favors the ball type.
There is an adjustable length pivot (shown) with an adjustment range of 1-3/8 to 1-1/2 inches available for GM engines that can sometimes be used to compensate for variations in flywheel, clutch disc, and release bearing thickness. More about this in the troubleshooting section.
Both ball and mushroom-head GM pivots are available in 1-3/8 and 1-1/2″ length (overall length when not [this is important] installed in the bellhousing). It is very important to use the correct style of pivot in relation to the type of arm being used.
Transmission Front Bearing Retainer
This great device has three critical functions. This first is as its name implies. The second is to provide a register on which the bellhousing must center. This is feature is sometimes overlooked with expensive consequences. Thirdly, its tubular snout is the surface on which the throwout bearing rides on its way in to depress the springs of the pressure plate. Conversions often require special and modified retainers to acheive compatibility.
Bellhousing
This provides a mounting place for the transmission, as well as a means of aligning the transmission to the engine. In some applications it also has a structural mounting function.
The alignment function is extremely important. Unfortunately, this is the most often overlooked and least understood part about the bellhousing.
Most people who have worked on these parts realize there are aligning pins in the engine block that register with holes in the bellhousing. What they do not realize is, there can be a variation in the location of these holes and this variation can affect clutch and transmission life. How to check bellhousing alignment will be covered in its own section further on in this article.
Clutch Linkage
This consists of everything between your foot and the clutch release arm. The linkags is the method of transferring the force of your left foot into the bellhousing and pressure plate release. The linkage can be mechanical, cable type or hydraulic. Note here that problems tend to show up because there are usually several choices of release arms and bearings for any particular family of engines. Choosing the wrong parts can get the linkage out of relationship and cause problems that can only be solved by removing the parts and starting over with other parts. The linkage cannot be made to compensate incorrect choice of release bearing or fork.
Cable Style Linkage
Cable linkages may seem appealing because it is easy to understand and simple to hook up. However, once past this, the installer may discover that it has high friction, stretches, sticks, rusts, freezes, frays and breaks. A cable type clutch should probably be the last choice of the three types of linkages.
Cable linkages work fine in smaller applications such as motorbikes and light cars, but they have an unsustainable record in light and heavy truck applications.
Some CJ & Commando Jeeps from 1972-1974 used a cable release, with subpar results as evidenced by the duration of their implementation.
Mechanical Style Linkage
Next is the mechanical linkage which is, with a few exceptions, the type found on the majority of Jeeps® built prior to 1987.
There are several basic styles of Jeep mechanical linkage but all are used in nearly their original configuration when doing an engine conversion. They usually consists of a pushrod at the pedal, a bellcrank and an additional pushrod actuating the fork. Earlier systems use pullrods, bellcranks and cables in lieu of pushrods, effectively reversing the way the systems works.
The mechanical linkage is largely a successful method of clutch release. One drawback obvious to many off-roaders is the tendency of some of these to bind during frame and powertrain flex and differentiation.