The Novak Guide to Clutches, Linkages & Bellhousings for Jeep® Conversions
Article provided by Novak Conversions – experts in Jeep conversions since 1967
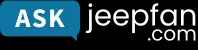
Get personalized content recommendations and answers drawn from our website. Simply type your question or topic of interest, and our AI assistant will help you find relevant articles, tips, and insights. You can also have a natural conversation to explore topics in more depth.
This article contains the culmination of decades of experience setting up clutch systems for Jeep conversion applications. We will first identify the components involved, and then introduce the science of setting up a proper clutch release system.
The flywheel provides a friction surface for the clutch disc, a torque buffering mass, a mounting surface for the pressure plate, a mounting for the starter driven gear, and on some engines the flywheel is a factor in engine balance.
The condition of the friction surface of the flywheel is important for proper clutch function. The surface should be smooth and free of burned spots and surface cracks. Used flywheels can be resurfaced. This should be done by grinding rather than lathe turning as less material is removed. The amount of material removed from the face can affect which clutch release bearing should be used. A flywheel should always be checked for runout on the engine it will be used on. Face runout should not exceed .005″ of an inch.
Pressure Plate
This is the other half of the driving friction surface. It mounts on the flywheel. It consists of four main parts and is more correctly called a clutch cover assembly. These parts are the pressure plate itself, the springs (or spring, if a diaphragm type), the clutch cover, and the release arms. There are two basic designs of clutches usually referred to by the spring type.
These are the Rockford™ (diaphragm spring type) and the Borg and Beck™ (coil spring type). The coil spring type is also called a three-finger type, referring to the three release arms this style requires to compress the coil springs.
The “softest” clutch is the diaphragm type. It also requires the least amount of travel to release. The diaphragm type clutch works good in lightweight, low geared vehicles. It is not the best clutch for high RPM use as the diaphragm spring will stay “flat” or released from the centrifugal force generated by the RPM. A variation of the diaphragm type was used for a while by GM, that to some extent helped this problem. This was called the Hi-Cone diaphragm type and was designed so the spring – instead of being flat when released – still had a slight bevel. These Hi-Cone units were not bad but still won’t hold like the Borg and Beck coil spring type. Aftermarket units like the Centerforce®, use centrifugal weights to counteract this high-rpm flattening and subsequent loosening. It should be noted that this is not typically a concern of the Jeep enthusiast as high RPM horsepower is not as much an interest as low-RPM torque. It should be pointed out that the spring itself is the “release arms” of a diaphragm type clutch. Note that when interchanging from one type to the other, you will require a different throwout bearing. The three-finger style requires a longer throwout vs. the diaphragm type, which uses a shorter throwout bearing. More on this later…
The fourth part of the pressure plate assembly is the cover. The pressure plate, spring (or springs) and release arms are attached to the cover in such a manner that, when the release bearing pushes on the three arms or the diaphragm spring, it causes a leveraged action to take place. This counteracts the spring pressure and lifts the pressure plate off the clutch disc, releasing the clutch.
As stated above, the diaphragm type clutch takes slightly less travel to release and requires about .030 total air gap when released. The coil spring type requires about .040 to .050 total air gap when released. Air gap is the clearance between the clutch disc, flywheel, and pressure plate with the clutch released. A total air gap of .050 will measure .025 between each side of the disc.
Clutch Disc
This is the “driven” part of the clutch. It has a friction material riveted to each side of a wavy spring (called a marcel). This is attached to a splined hub that the transmission input gear protrudes into.
There are basically two common types of friction material used for clutch lining. These are organic and metallic. The organic is best for all around use. The metallic is preferred by some for severe duty applications but requires high spring pressures and is hard on the flywheel and pressure plate friction surfaces. Avoid solid hub clutches and clutches without marcel as they will always chatter when used in vehicles with a rear differential mounted on springs (as opposed to a transaxle design).
Pilot Bushing
In most cases, this is a porous bronze, pre-lubed bushing rather than an actual bearing, as it is often called. A few applications still use an actual bearing and others use a needle roller type bearing, but by far, the most common type is bronze. You cannot use a roller bearing on a transmission shaft originally designed for a bronze bushing due to different type of heat treatment on the shafts.
For a list of several versions of pilot bushings offered by Novak, jump here.
The pilot bushing is seldom thought of as a part of the clutch system but it is one of the most vital parts of the system. It pilots the end of the transmission input gear in the crankshaft. If it is worn or not running “true”, it can cause serious clutch problems or transmission failure. Pilot bushing bore runout should always be checked with a dial indicator and should be within .002 total. The bronze bushing type should be a press fit in the crankshaft bore. It must be installed carefully. It should have between .002 and .003 clearance on the transmission shaft when installed. The pilot bushing is only functional when the clutch is disengaged but it is a factor in input gear alignment at ALL times.
Most people have no idea what an important part the pilot bushing plays in the life of the transmission and clutch. The job of the pilot bushing is to support the end of the transmission input (main drive) gear in the crankshaft and it only acts as a bushing when the clutch is depressed. This pilot bushing should be a light drive fit into the crank bore. Care should be taken when installing any pilot bushing as they are soft and easily damaged by crude installation techniques. A damaged pilot bushing can bind on the input gear giving symptoms of clutch drag. Transmission damage and early failure can be caused by a pilot bushing or crankshaft bore that “runs out” in relation to the transmission locating bore in the bellhousing. It is advisable to check the bore of the crank with a dial indicator before installing the pilot bushing (see below). If the bore runs out more than .003 total, the crank should be set up in a lathe and the bore trued up OR a special pilot bushing should be made that runs out the same amount as the crank bore. The run out in the bore of a pilot bushing is put 180 degrees off from the crank bore run out and the pilot bushing installed. If properly done, this can put the bore of the pilot bushing well within the .003 required. We have used this method to save engine disassembly many times. A disadvantage of this method shows up at pilot bushing replacement time as a special pilot bushing will have to be reproduced.
It is always a good idea to use an input gear (of the proper diameter) or clutch aligning tool when installing the clutch on any engine. With the clutch disc aligned on the pilot bushing it becomes a simple matter when installing the transmission to engage the splines and bolt up the transmission . If this simple procedure is not done, the transmission shaft won’t line up and the temptation will be great to “pull it up with the bolts” which damages the front transmission bearing, pilot bushing, and more than likely will break an ear off the transmission or adapter. The transmission should slip in freely to mate up with the face of the bellhousing.